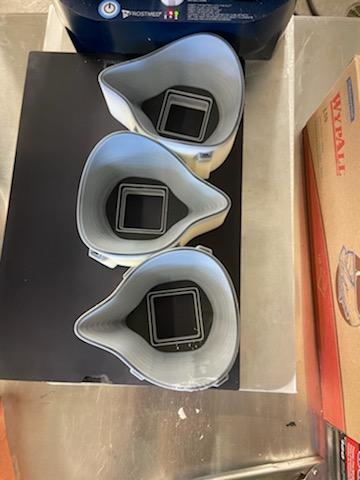
The prototype masks the NDSU research team has made.
A group of students are giving back to the community by making prototype masks
As of March 31, there have been 122 people in North Dakota who have tested positive for the coronavirus (COVID-19). Three people in the state have died due to the virus and underlying health conditions. Two of these cases were contracted via community spread.
At present, North Dakota does not face the same medical supply shortages as other hospitals in the country, but local institutions want to have proactive responses to a potential spike in cases.
N-95 masks are used as respiratory protective equipment for higher-risk procedures or more contagious patients. They contain a filter that blocks most airborne droplets, including COVID-19, from reaching the face. These masks also inadvertently deters one from touching their face with their hands.
Across the country, states are experiencing shortages of N-95 respirator masks. A local physician wanted to help alleviate this problem and challenged NDSU to create a reusable respirator mask to be used by healthcare workers to protect them from exposure to COVID-19.
Mechanical Engineering graduate students, Dallas Patton and Joseph Fehrenbach, along with undergraduate, Laura Friedmann, accepted the challenge. They are currently manufacturing prototype masks and are working on a process to create their own filter material for the masks.
The researchers are exploring different materials for use as the filter. The prototypes will be fitted with electrospun polypropylene fibers rated at MERV15 filtration level, meaning they have an equivalent filtration level to that of the N-95 mask that is currently being used by healthcare workers fighting the coronavirus.
The prototype masks are currently being 3D printed with a flexible, crosslinked, elastomer material. The researchers are also exploring printing with a different material, thermoplastic urethane (TPU).
Friedman said, “The masks printed with TPU cost about $3 to print but are lower in quality and may not provide an adequate seal around the face, while the mask printed with the elastomer material cost roughly $70 to print and are providing a very good seal around the face.”
Fehrenbach, Friedmann and Patton are working on using a material that is both cost-effective and provides the highest level of safety to protect from respiratory illnesses.
The research team plans to complete their prototype of the respirator mask this week. Once they complete some of their prototypes, they will send them to a local hospital for testing and evaluation. If the masks function effectively, more masks will be manufactured by NDSU to be tested at local hospitals.
Manufacturing is currently taking place in NDSU labs, but they are looking to partner with local manufacturers to speed the production.