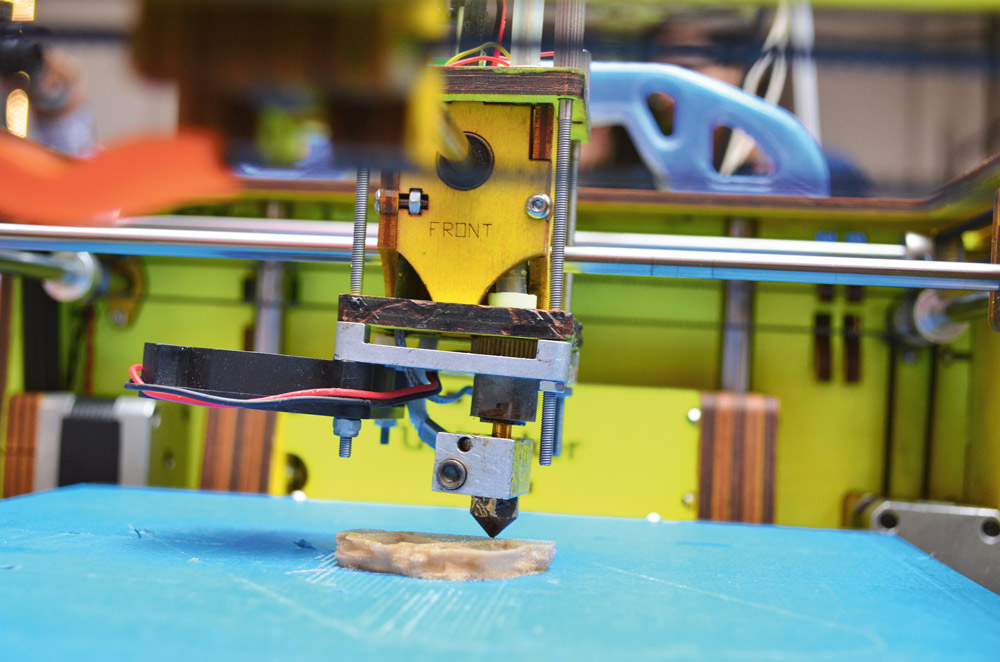
3D printing is an up and coming art form that is extremely useful in making models.
Eleven years ago, Ben Bernard wanted to bring something life-changing to students at North Dakota State.
“Architecture students must do lots of model making,” he said. “Traditionally, it’s done by hand and takes many hours. It blew my mind how much work the poor students have to do.”
The computer service specialist began to research technology that would make work more productive and allow rapid prototyping for students. He learned about 3-D printing: using a computer-controlled plastic extruder, a 3-D printer can build up objects layer by layer until complete.
In 2007, 3-D printing was expensive and slow. A cubic inch of filament (the necessary “ink” for the printer) cost $5, and it cost over $20,000 for the machine.
“Industrial and Mechanical Engineering had a machine,” Bernard said. “We put together a proposal to expand 3-D printing within the college but couldn’t secure the funding.”
Luckily, this didn’t stop Bernard from pursuing the technology.
In 2013, two classroom-ready 3-D printers were purchased. Bernard and his students broke and fixed the printers, discovering how they worked and how they could use them to their best advantage.
“It was amazing what students could do with the 3-D printers,” Bernard said. “They could design and print complex 3-D shapes you couldn’t design any other way. It was a good way to represent ideas and bring them into the world.”
3-D printing has quickly spread across campus: Architecture and Landscape Architecture’s lab now totals ten 3D- printers to meet student demand and many other departments have added their own. The Development Foundation’s Impact Fund Grant helped to create a 3-D printing service at the Main Library accessible to all NDSU students, staff and faculty for a rate of $3 per print hour.
Bernard continued, “This is really unique to NDSU. A lot of other universities have their students paying up to $20 per hour, or they’re only accessible to grad students.”
Right now, NDSU uses PLA, a material made from a corn starch derivative. It’s non-toxic and highly sustainable.
“The plastic we use is an agriculture product, which makes it especially cool because of the strong agriculture ties NDSU has,” Bernard said.
Both student and faculty success has come from NDSU’s adoption of 3-D technology, too.
In 2015, the Innovation Challenge winners of the SkyHawk team used 3-D printing to prototype parts for their drone designs. The runner-ups, Amber Grindeland and Caet Fox, used 3-D printing to create innovative clothes hangers.
In 2012, John Schneider, with M-State alum Jake Clark, founded Fargo 3-D Printing with their experience at NDSU.
NDSU engineering students now work on how to build affordable prosthetics for children, revolutionizing the world of medicine and making the lives of families easier.
Chad Ulven in the Department of Mechanical Engineering works on 3-D printing filaments that are produced from recycled materials.
Bashir Khoda is the Director of Additive Manufacturing Research Laboratory in the Industrial and Manufacturing Engineering Department. Khoda is the lead on a bio-additive manufacturing group with the objective of functional organ and tissue printing. His group is working on designing a 3-D printing of lightweight cellular structures and on tablets for personalized medication.
“3-D printing makes it easy to create for very little cost, making it perfect for rapid prototyping. The improvement cycle can take place over hours instead of months. This allows entrepreneurs to market faster and designers to discover faster,” Bernard said.
The implications for 3-D printing are nearly endless: it covers a broad range of topics, from medicine to machinery to mindless baubles.
If you’re not brilliant in design, the website thingiverse.com allows you to easily upload and download designs from people around the world. This allows students from a variety of colleges to experiment with the technology.
“It’s fun to see how 3-D printing has been used as a design, research, and education tool,” Bernard said.
Looking forward to see the dramatic improvement of artificial limb, joints etc supplied to the poor with no cost.